I've learned more about this issue, and have come up with an experimental solution...
Here are the removable pieces involved, disassembled...
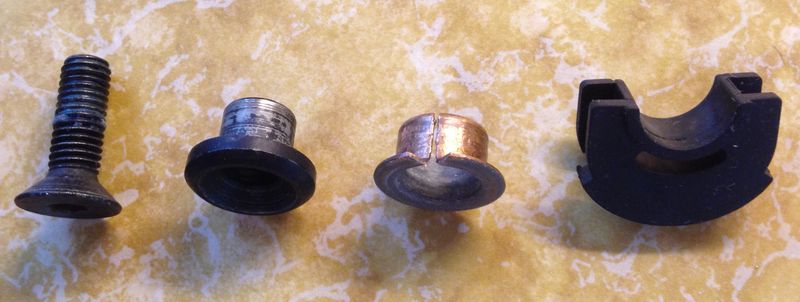
To the inside of the rubber piece, there is a free-rotating copper bushing, and then a steel piece, which the screw, when tightened, fixes into position so it can't rotate.
The problem, as best I can understand, is inadequate axial clearance for the rubber bushing. Notice the rubber piece is sticking out a little over 2mm past the end of the fixed steel sleeve:
This lack of clearance pinches the rubber bushing, causing friction and accelerating its wear. I have no idea why the assembly would be designed this way. (Maybe the rubber piece was updated with thicker dimension, but other updated parts in my assembly are outdated/older style?)
My experimental solution to allieviate the rubber pinch is fabricating a thin aluminum spacer. It's a bit over 2mm thick:
(A side note on lubrication: I think Lubricating the outer edges of the rubber bushing was also a bad idea - the piece should not move with respect to the piece it's inserted in. The inner area of the rubber bushing rotate mostly on the copper sleeve, so seems like lubrication is optional. Lubricating between steel and copper pieces pretty clearly seems like a good idea
Here is how the assembly (with experimental spacers) looks like all put together: