Quick update:
I have a new coolant pump, and the accuracy of my cnc turning center have never been better! Seriously, the Acetal dust from previous machining got stuck in a small T pipe in-the-tool-turret... as-in where the coolant comes out :/ Long story short, I have a new pump! and clean turret internals (and wasted 1.5 full day/night of work)
Other than that, got 986 million adapters fully machined. And yes I've "vacuum" the milling center this time. Can't afford another of those pump lolll
Inspection on the adapeter next (once they are cleaned) and we are done with that part! I'll let you know how many failed lollll
In a meantime, I'm doing the center aluminum caps this Wed, Thurs and Fri!
In the Media this week:
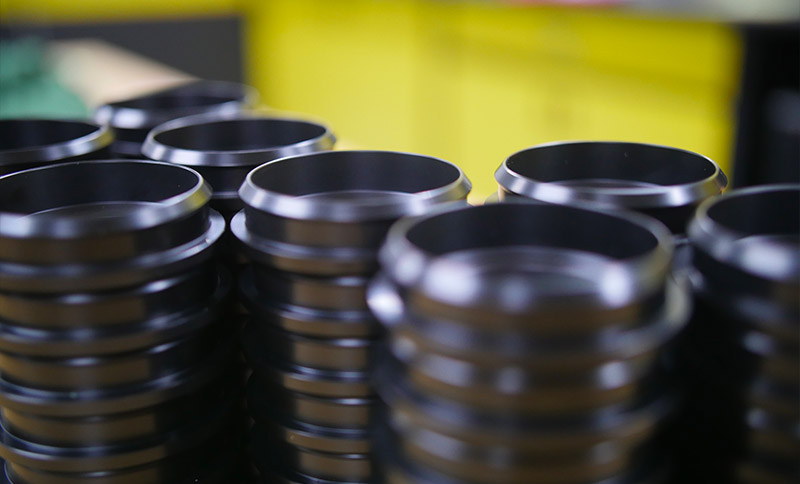
^ Got a few more than a few of those adapters. Hopefully they will all be within the 0.05 tolerance/spec after inspection. For a 4 (four) operations part, that'd be a miracle lolll
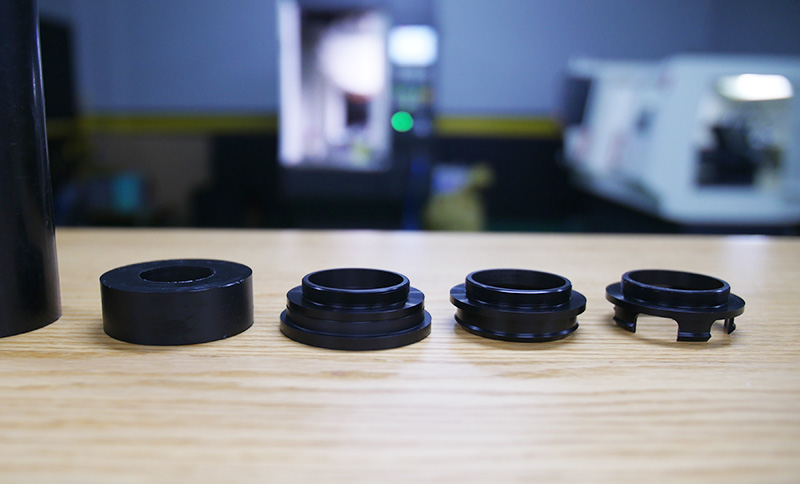
^ The Great Porsche Center Cap is not all that easy to do. Following pic showing the 3 lathe operations + 1 multi-axis milling... and that is just for the adapter!
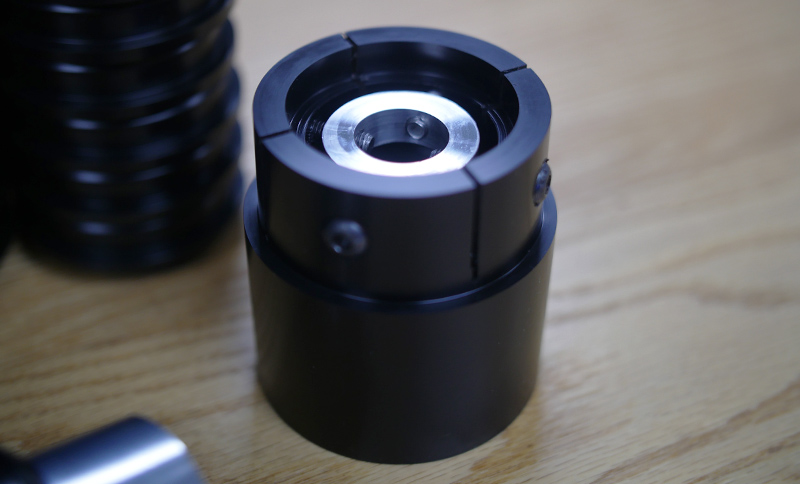
^ Custom precision fixture to machine the third op. This is the most critical as we need parallelism and concentrically down to 0.05mm precision. The four screw do just that... adjust the concentrically (trade secrets online, there you go...)

^ Done with the Acetal! That machine needed a serious clean-up :/ Acetal is fun to machine but got to be vacuum after... so I've recently learn :/
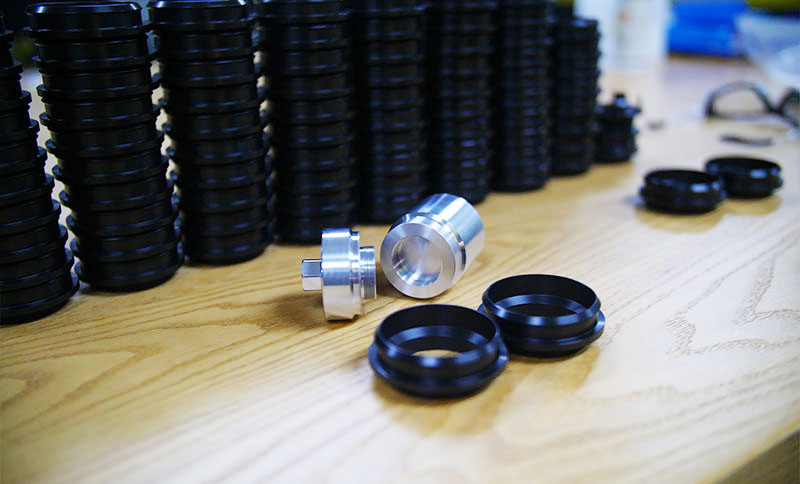
^ Moving to the last operation (multiaxis milling). Following 3 pics are visuals of the another custom precision fixture (jig). These fixtures just take 1.5 days to do sometimes... they are as good as the required precision of the part they accommodate.
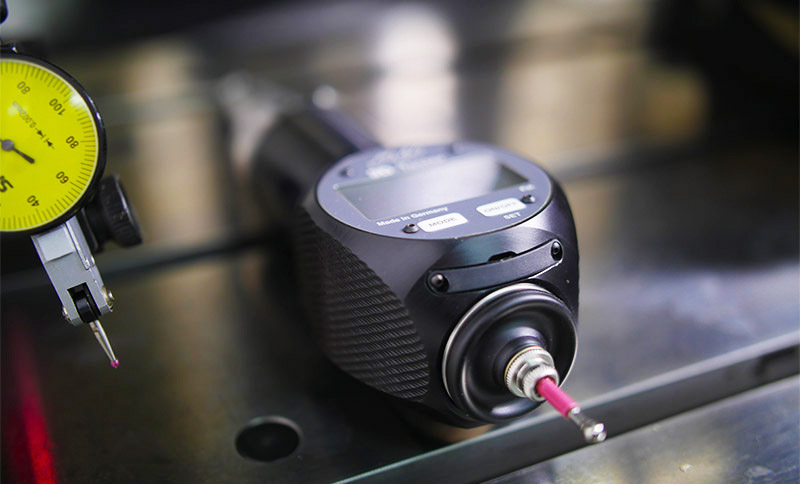
^ Favorite tooling for dialing the 4axis and fixture. All have to be withon 0.05mm. Ridiculous for a center caps I know but hey... they are for Porsche cars