The tool i devised consists of a piece of 1/4-20 all thread, an acorn nut, a piece of 1/2" copper pipe (which is about 5/8 OD), a piece of fuel hose and a few more 1/4-20 nuts.
I first did a mock up as follows
Basically this is a Chinese finger puzzle, or viewed another way out is similar to the way some of you extract your spark plug tubes. Picture a small diameter boat drain plug on an extension.
I had hoped to find a socket which would slip inside the copper pipe. I would have sacrificed a cheap socket for the cause. That size combination didn't materialize, so i ended up bonding a nut in the end of the tube using JB Weld. In addition, the rubber piece on the finished product is around 2" long. As shown it wouldn't get past the deep chamfer in the wrist pin.
The diameter of the copper is required to retain the wrist pin when it comes out of the bore.
It worked perfectly.
Above picture taken down the cylinder bore after the wrist pin was extracted. This shows how the clip is kept from dropping inside the engine.
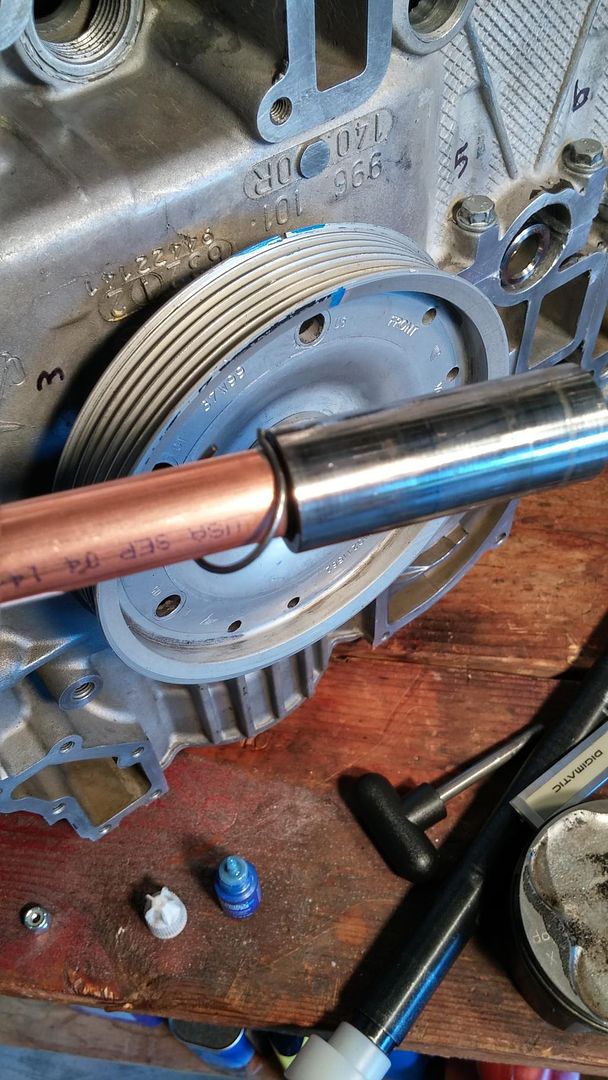
Extracted.
Half an hour later i was done installing the last of my pistons.
Huge relief to have that behind me.